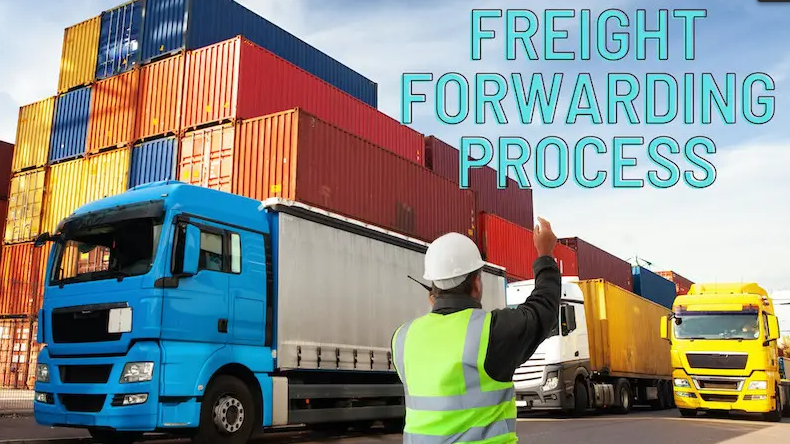
Investigation of root causes of order unfulfillment: A Logistics case study
This study targets an order fulfillment problem in a freight forwarding company. Some applicable solutions are implemented such as supplier performance evaluation, suppliers' selection, and location analytics. The objective of the study is to reduce the number of unfulfilled orders by supply planning. Some of the tools used to achieve this are Excel (VBA and Pivot tables) to perform drivers' scoring, analytic hierarchy process (AHP), and ArcGIS software to visualize locations. The results showed that the company can implement the suggested solutions to reduce the number of order cancellations and assist drivers based on clients' demands to ensure customer satisfaction and loyalty. The AHP allows the company to standardize the order fulfillment process, keep clients' loyalty, satisfy clients' demands and eliminate a random selection of drivers. In addition, drivers' evaluation can assist the company to visualize drivers' performance through the five different criteria: punctuality, truck quality, reliability, appearance, and mobile app usage in different periods of time and assign the drivers to new clients based on their scores to avoid any complaints from clients. For the map visualization, it matches supply with demand as currently, the company acquires suppliers with no strategic purpose. The locations visualized on the map assist the supply team to indicate the regions that need an increase in the capacity of contractors and drivers close to the client's location. In addition, the map illustrates the business size and territory. © 2021 IEEE.